Waste Minimization Techniques in Plastic Injection Moulding
- Shraddha Srivastava
- Mar 18
- 4 min read
Introduction
Plastic injection moulding is one of the most efficient and widely used manufacturing processes, yet it still faces significant material wastage issues. Studies show that up to 30% of raw polymer material in traditional injection moulding processes is wasted due to inefficient sprue and runner systems, rejected parts, and overproduction. With increasing regulatory scrutiny and material cost pressures, implementing Waste Minimization Techniques in Plastic Injection Moulding has become a top priority for manufacturers.
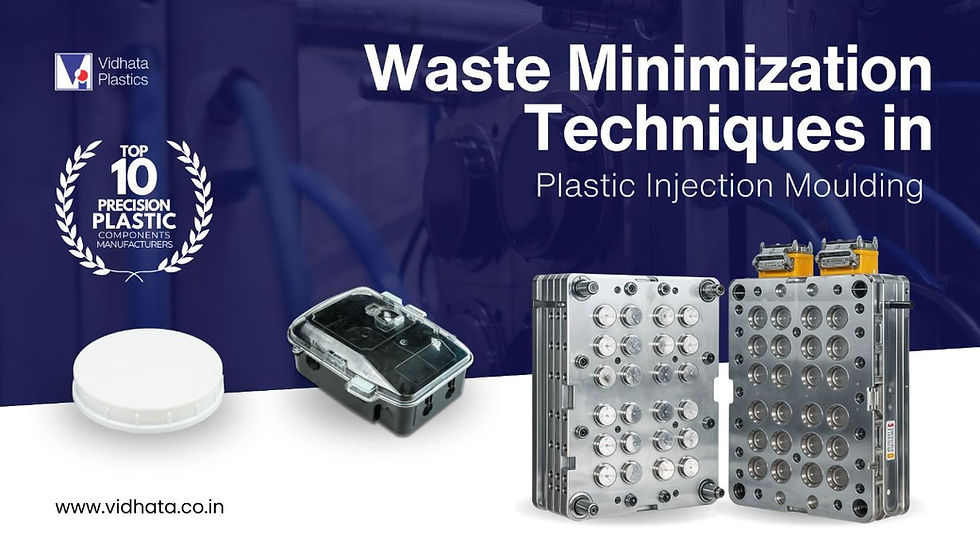
Waste reduction in injection moulding requires advanced process control, precision engineering, and real-time optimization. From high-performance hot runner systems to AI-driven defect prevention, technological innovations are reshaping waste minimization strategies.
As a leading plastic parts manufacturer in India, Vidhata Plastics utilizes cutting-edge Waste Minimization Techniques in Plastic Injection Moulding to optimize efficiency, reduce material loss, and ensure sustainability. This blog explores the root causes of waste, advanced waste reduction strategies, and how Vidhata Plastics is pioneering low-waste, high-precision injection moulding solutions.
Sources of Waste in Plastic Injection Moulding
1.1 Runner and Sprue Waste in Cold Runner Systems
Conventional cold runner moulds generate excessive waste, as the sprue and runners account for 15–40% of total material usage in each cycle.
Material regrind limitations affect polymer properties, restricting reuse percentages for high-performance applications.
1.2 Process-Induced Defects Leading to Scrap Parts
Sink marks, warpage, and short shots are caused by improper cooling rates or melt flow inconsistencies.
Burn marks and flash defects due to excessive shear stress and poor venting, leading to material degradation.
Molecular degradation from thermal cycling, reducing polymer chain length and mechanical strength, resulting in rejected parts.
1.3 Energy & Resource Inefficiencies
Suboptimal cycle times and inefficient clamping forces increase machine wear, requiring higher energy input.
Inconsistent melt temperature control leads to overcompensation with excessive heating or cooling, increasing process inefficiencies.
Advanced Waste Minimization Techniques in Plastic Injection Moulding
2.1 High-Performance Hot Runner Systems for Zero Runner Waste
Cold runner moulds produce up to 30% excess plastic per cycle, whereas hot runner systems eliminate runner waste by delivering molten plastic directly into the mould cavity.
Valve-gated hot runners allow controlled sequential injection, reducing pressure variations and improving flow balance.
Pressure-compensated manifold designs ensure uniform cavity filling, reducing defect rates and rework costs.
2.2 AI-Driven Process Optimization for Real-Time Waste Reduction
Machine learning algorithms analyze real-time sensor data to dynamically adjust injection speed, holding pressure, and cooling times.
In-line rheology monitoring detects viscosity fluctuations, preventing defective parts before they form.
Automated closed-loop feedback systems adjust parameters within milliseconds to maintain consistent shot weight and dimensional accuracy.
2.3 Advanced Mould Engineering for Material Efficiency
CAE-based simulations (Moldex3D, Autodesk Moldflow) optimize gating, venting, and cooling system layouts, reducing material overuse.
Multi-cavity moulds increase production yield per cycle, maximizing material utilization efficiency.
Conformal cooling systems enhance heat transfer uniformity, preventing warpage and improving cycle consistency.
2.4 Sustainable Material Utilization & Recycling Integration
Regrind optimization algorithms allow controlled reuse of sprues and runners, maintaining polymer integrity.
Reactive polymer compounding introduces chain extenders to restore mechanical properties in recycled materials.
Hybrid material blends (recycled polymers + virgin resins) maintain performance without compromising sustainability.
2.5 Energy Optimization in Injection Moulding Machines
Servo-electric machines consume up to 60% less energy than hydraulic systems while delivering precise shot control.
Dynamic cooling flow regulation minimizes energy-intensive cooling times, optimizing thermal efficiency.
Vacuum-assisted degassing in high-precision moulds reduces purge waste while improving part consistency.
How Vidhata Plastics Implements Waste Minimization Techniques in Plastic Injection Moulding
As an industry leader and a top plastic injection mould manufacturer in India, Vidhata Plastics has developed a comprehensive waste minimization framework that integrates precision engineering, AI-driven process control, and sustainable material utilization.
Hot Runner Optimization:
Valve-gated hot runners eliminate 98% of runner waste, enabling near-zero material loss per cycle.
Rheologically balanced manifold designs ensure uniform polymer distribution, preventing overflows and shot inconsistencies.
Automated Defect Prevention & Quality Control:
AI-based real-time defect detection identifies and corrects processing anomalies before defective parts are produced.
Thermal imaging sensors and ultrasonic cavity inspection ensure the melt uniformity and structural integrity of the final part.
Sustainable Polymer Processing:
Closed-loop material recovery systems allow up to 30% regrind incorporation without mechanical degradation.
Reactive extrusion and compatibilizers enhance material properties in recycled resins, maintaining high-strength performance.
High-Efficiency Mould Design & Process Optimization:
Precision gate placement and venting engineering reduce burn marks, warpage, and short shots.
Cycle time optimization algorithms shorten cooling phases, reducing energy waste without compromising part quality.
By implementing these cutting-edge waste minimization strategies, Vidhata Plastics reduces raw material consumption, lowers defect rates, and enhances production efficiency, making it a benchmark in sustainable plastic parts manufacturing in India.
The Impact of Waste Minimization in Injection Moulding
4.1 Cost Reduction & Resource Efficiency
Material consumption was reduced by up to 30%, directly lowering production costs.
Optimized cooling and cycle times decrease energy usage by 40% per moulding cycle.
4.2 Improved Sustainability & Regulatory Compliance
Supports ISO 14001 environmental management standards for sustainable manufacturing practices.
Meets EPR (Extended Producer Responsibility) mandates and aligns with global carbon reduction initiatives.
4.3 Superior Product Quality & Performance Consistency
AI-driven process control eliminates dimensional inconsistencies, ensuring higher yield rates.
Optimized injection parameters improve structural integrity, minimizing post-processing waste.
4.4 Energy Conservation & Carbon Footprint Reduction
Smart mould temperature control systems reduce thermal losses, cutting CO₂ emissions by 50%.
Electric servo-driven moulding machines consume significantly less energy compared to their hydraulic counterparts.
Conclusion:
The future of plastic injection moulding depends on waste minimization, efficiency, and sustainability. By implementing state-of-the-art process optimization, AI-driven defect prevention, and high-performance mould engineering, manufacturers can significantly reduce material waste, improve operational efficiency, and lower environmental impact.
As a trusted mould manufacturer in India, Vidhata Plastics excels in precision-driven, sustainable injection moulding solutions. If you're seeking a plastic parts manufacturer in India that prioritizes waste minimization, energy efficiency, and advanced mould design, partner with Vidhata Plastics today.
Contact us now to learn how our expertise in Waste Minimization Techniques in Plastic Injection Moulding can enhance your production efficiency and sustainability goals.
Visit Our Website: https://www.vidhata.co.in/
Contact Us: https://www.vidhata.co.in/contact
Email Id: info@vidhata.co.in
WhatsApp No. : +919550665666
Comments