How Smart Polymers in Medical Plastic Parts Are Saving Lives
- Shraddha Srivastava
- Mar 28
- 5 min read
Introduction
The integration of smart polymers in medical plastic parts is transforming modern healthcare, enabling responsive, adaptive, and high-performance medical devices. The global medical plastics market is projected to reach $89 billion by 2028, driven by the increasing demand for biocompatible, antimicrobial, and shape-memory polymers in medical applications.

As medical technology advances, plastic parts manufacturing has shifted towards intelligent polymer solutions that enhance drug delivery, surgical precision, and implant durability. Smart polymers in medical plastic parts exhibit stimuli-responsive properties, enabling them to change shape, release drugs, or self-heal based on temperature, pH, or biological signals.
This blog explores the latest advancements in medical plastic parts, focusing on biomedical applications, polymer innovations, and manufacturing challenges.
Understanding Smart Polymers in Medical Plastic Parts
1. Defining Smart Polymers in Biomedical Engineering
Smart polymers, or stimuli-responsive macromolecules, undergo precise physicochemical transitions in response to external stimuli, optimizing biomedical device performance. Their molecular architecture allows reversible phase changes, triggered by:
Thermoresponsive Polymers – Phase-separating at critical solution temperatures (LCST/UCST) for controlled drug release.
pH-Responsive Polymers – Ionizable groups regulate drug solubility and bioavailability in tumor-targeted delivery.
Electroactive & Magnetoresponsive Polymers – Enable biosensors, neural prosthetics, and remotely controlled implants.
These next-gen polymer systems enhance adaptive performance and biocompatibility in medical plastic parts.
2. Key Smart Polymers in Medical Plastic Parts
a. Shape-Memory Polymers (SMPs)
Engineered with segmented domains, SMPs restore pre-set geometries upon thermal, moisture, or enzymatic activation.
Applications:
Self-expanding vascular stents (biodegradable polyurethane SMPs).
Thermally activated orthopedic fixation devices for fracture stabilization.
Smart sutures with adaptive stress relaxation properties.
b. Hydrogels
Hydrophilic, crosslinked networks with osmotic swelling behavior, allowing controlled therapeutic release and tissue integration.
Applications:
Injectable bioactive wound dressings promoting angiogenesis.
Artificial corneas with IPN structures for mechanical resilience.
pH-sensitive hydrogels for targeted drug delivery.
c. Conductive Polymers
π-Conjugated polymers (PANI, PPy, PEDOT) facilitate biocompatible electronic interfacing for biosensors and neural implants.
Applications:
Electroactive scaffolds for neural regeneration.
Polymeric electrodes in DBS implants for neuromodulation.
Wearable biosensors for real-time health monitoring.
d. Biodegradable Smart Polymers
Designed for controlled bioresorption, these polymers feature predictable degradation kinetics for implants and regenerative medicine.
Applications:
PLGA nano-carriers for oncological drug release.
Self-dissolving hemostatic films for rapid clotting.
Tissue scaffolds promote gradual cell differentiation.
Steps in Manufacturing Medical Plastic Parts with Smart Polymers
The fabrication of medical plastic parts using smart polymers requires high-precision processing methodologies to maintain biocompatibility, structural fidelity, and stimuli-responsive behavior. Key phases include:
1. Polymer Selection & Advanced Material Engineering
Identification of stimuli-responsive polymeric architectures based on targeted biomedical functionalities (e.g., thermoresponsive hydrogels for site-specific drug release, shape-memory polymers for self-expanding implants).
Nanocomposite formulation integrates bioceramics, conductive fillers, and antimicrobial nanoparticles to enhance mechanical reinforcement, electroactive properties, and biointerface compatibility.
Validation of molecular weight distribution, crosslinking density, and degradation kinetics to comply with FDA, ISO 10993, and USP Class VI biocompatibility benchmarks.
2. High-Precision Plastic Injection Moulding
Micro-injection moulding for sub-millimeter biomedical microstructures, optimizing polymer melt viscosity, shear rate, and mold cavity replication fidelity.
Multi-material co-moulding enables seamless integration of functionalized smart polymer layers (e.g., gradient-drug releasing implants).
Nano-imprint lithography (NIL) and laser-assisted moulding to generate sub-micron bioactive surface topographies, enhancing cell adhesion and tissue integration.
3. Surface Functionalization & Bioactivation
Plasma-enhanced chemical vapor deposition (PECVD) and UV-induced photografting to functionalize polymeric surfaces, optimizing wettability, protein adsorption, and biointeractivity.
Covalent grafting of bioactive ligands (e.g., RGD peptides, heparin, or antimicrobial agents) for targeted cellular interactions and infection resistance.
Crosslinking kinetics control in hydrogel matrices to regulate swelling dynamics and drug release kinetics in hydrogel-based medical coatings.
4. Precision Metrology & Performance Validation
Atomic Force Microscopy (AFM) and Scanning Electron Microscopy (SEM) for sub-nanometer structural characterization and topographical mapping.
Fourier Transform Infrared Spectroscopy (FTIR) and Raman Spectroscopy to assess polymer chain integrity, functional group modifications, and chemical bonding interactions.
Dynamic Mechanical Analysis (DMA) and Differential Scanning Calorimetry (DSC) to optimize viscoelastic behavior, thermal transitions, and polymeric phase stability under physiological conditions.
Cytotoxicity assays and accelerated biodegradation profiling for long-term in vivo biocompatibility assessment.
5. Sterilization & Contamination-Controlled Packaging
Ethylene oxide (ETO) gas sterilization for sensitive polymeric structures, ensuring low-temperature microbial inactivation without polymeric degradation.
Gamma irradiation with dose-controlled polymer resilience mapping to preserve molecular weight distribution and mechanical integrity.
Class 100 cleanroom assembly and nitrogen-purged packaging for particulate-free delivery and extended material stability.
This multi-disciplinary manufacturing approach ensures smart polymers in medical plastic parts retain functional adaptability, regulatory compliance, and long-term performance in biomedical applications.
Applications of Smart Polymers in Medical Plastic Parts
1. Smart Drug Delivery Systems
Smart polymers in medical plastic parts enable targeted and controlled drug release, improving treatment efficacy while minimizing side effects.
pH-responsive capsules release cancer drugs at tumor sites, reducing systemic toxicity.
Temperature-sensitive hydrogels control the release of insulin for diabetic patients.
Magnetically responsive polymers enhance precision drug administration in chemotherapy.
2. Minimally Invasive Surgical Devices
The advancement in medical plastic parts has led to the development of self-expanding and adaptive surgical tools:
Shape-memory polymer stents that expand after insertion, reducing surgical complications.
Biodegradable implants that gradually dissolve, eliminating the need for secondary surgeries.
Soft robotic grippers made from smart polymers for precise surgical manipulation.
3. Smart Wound Healing & Tissue Engineering
Electrically conductive smart dressings accelerate wound healing by promoting cell regeneration.
3D-printed smart polymer scaffolds guide tissue regrowth for organ repair.
Self-healing hydrogels provide antibacterial protection and improve chronic wound management.
4. Wearable & Implantable Biosensors
The development of flexible, lightweight biosensors using smart polymers has enabled:
Continuous glucose monitoring patches for diabetes management.
Real-time cardiac monitors with self-adaptive polymer substrates.
Smart contact lenses that detect glucose levels in tears.
Challenges in Manufacturing Smart Polymers in Medical Plastic Parts
1. Precision Plastic Injection Moulding
Manufacturing smart polymers in medical plastic parts requires high-precision plastic injection moulding techniques, such as:
Micro-injection moulding for miniaturized medical devices.
Multi-material moulding for integrating stimuli-responsive layers.
Nano-textured moulding to enhance cell adhesion in biomedical implants.
2. Material Stability & Processing Constraints
Smart polymers exhibit sensitivity to temperature and processing conditions, requiring optimized melt processing techniques.
Crosslinking control is critical to maintaining reversible phase transitions in responsive polymers.
3. Biocompatibility & Regulatory Compliance
Medical-grade smart polymers must comply with FDA, ISO 10993, and USP Class VI standards.
In-vitro and in-vivo testing is necessary to validate long-term safety and performance.
Smart Polymer Medical Parts Manufacturing by a Plastic Parts Manufacturer in India
As a leading plastic parts manufacturer in India, Vidhata Plastics specializes in the development of smart polymers in medical plastic parts for high-precision healthcare applications.
Why Choose Vidhata Plastics?
✔ Advanced plastic injection moulding for complex medical devices.
✔ Expertise in shape-memory, biodegradable, and conductive polymers.
✔ Strict compliance with international medical-grade plastic standards.
✔ Custom material formulations for enhanced biocompatibility and performance.
We collaborate with medical device manufacturers to produce high-performance, nano-engineered, and adaptive polymer components for next-generation healthcare solutions.
Conclusion
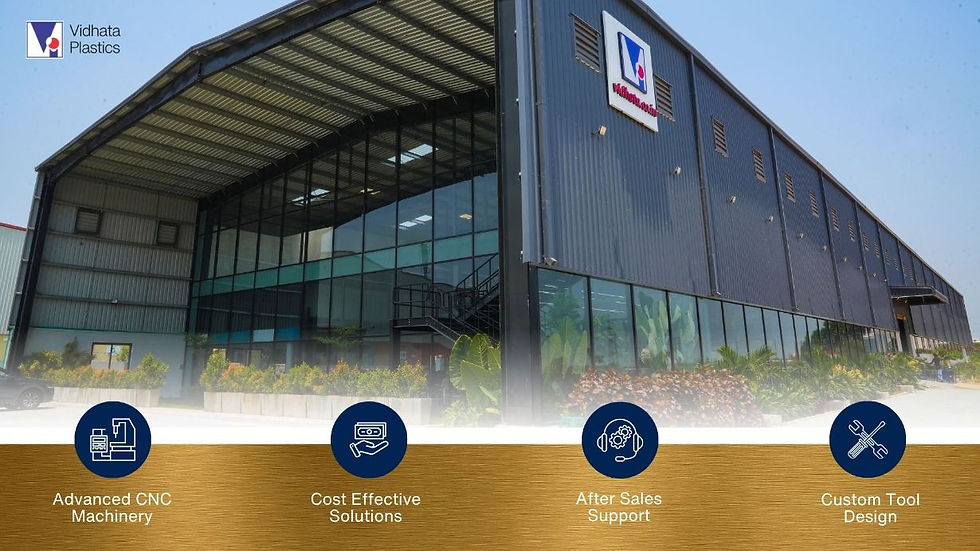
The advancement in medical plastic parts through smart polymers is revolutionizing healthcare by enabling adaptive, self-regulating, and biocompatible medical devices. From intelligent drug delivery systems to minimally invasive surgical tools, smart polymers in medical plastic parts are paving the way for safer and more efficient patient care.
At Vidhata Plastics, a trusted plastic parts manufacturer in India, we are committed to pushing the boundaries of medical plastics innovation, providing cutting-edge solutions tailored to the stringent demands of the healthcare industry.
📞 Contact Vidhata Plastics today to explore custom solutions in smart polymer-based medical plastic parts!
Visit Our Website: https://www.vidhata.co.in/
Contact Us: https://www.vidhata.co.in/contact
Email Id: info@vidhata.co.in
WhatsApp No. : +919550665666
Commentaires